
Teukho: In die Zeit Gemeißeltes Design
Lernen Sie Teukho kennen, Holzarbeiter in dritter Generation, die dafür bekannt sind, moderne Kreationen aus jahrtausendealtem, versteinertem Eichenholz zu fertigen. Entdecken Sie die mystische Schönheit dieses uralten Materials, das dank des exquisiten Geschmacks der Familie Garzitto für modernes Design in zahlreichen Formen neu erfunden wurde.
Der Inhalt dieser Seite wurde automatisch übersetzt. Besuchen Sie die Website auf Englisch
Teukho fängt Einblicke in längst vergangene Epochen ein und verwandelt sie in Kunst. Sie sind moderne Träger der Geschichte und zeigen die ursprüngliche Schönheit des fossilen Eichenholzes in allen ihren Kreationen. Der Name leitet sich vom altgriechischen Wort "Teúkhō" ab, das "kunstvoll gestalten" bedeutet.
Die Familie Garzitto, die in dritter Generation in Friaul-Julisch-Venetien verwurzelt ist, hat sich zu einem visionären Vorreiter in der Verarbeitung von fossilem Holz entwickelt, einem einzigartigen Material mit einer jahrtausendealten Geschichte. Die Kombination dieses essentiellen Elements mit einer zeitgenössischen Design-Sensibilität spricht für die Kunstfertigkeit, die hinter den meisterhaften, von den Formen der Natur geformten Werken von Teukho steht.
Lernen Sie die Kunsthandwerker hinter der Marke in einem aufschlussreichen Interview kennen, in dem es um die Ursprünge von Teukho, die Holzbearbeitung, die Natur des fossilen Holzes und die Bedeutung der Nachhaltigkeit geht.
Das Holz, das wir verwenden, stammt von Bäumen, die durch natürliche Ursachen umgestürzt sind und von Sedimenten begraben wurden, so dass ihnen der Sauerstoff entzogen wurde. Auf diese Weise bleibt das Holz über Tausende von Jahren hinweg erhalten.
Entstanden aus der Kreativität der Familie Garzitto, erzählt Teukho die Geschichte von versteinertem Holz und zelebriert die Liebe zu diesem Urelement und der Region Friaul. Wie wurde Ihre Marke ins Leben gerufen?
Der Unternehmergeist liegt in unserer DNA. Im Jahr 1960 gründeten unser Vater und unser Onkel ein Sägewerk, das Halbfertigprodukte für die aufstrebende Stuhl- und Möbelindustrie in Friaul herstellte und schnell zu einem der wichtigsten Akteure in diesem Sektor wurde. Von klein auf hörten wir von Holz und hatten die Gelegenheit, die verschiedenen Produktionsphasen von Halbfertigprodukten hautnah mitzuerleben: Das hat uns eine natürliche Liebe zum Holz eingeflößt, einer Essenz, die Wärme vermittelt und schon immer Teil des menschlichen Lebens war.
Auf unseren Reisen auf der Suche nach neuen Bezugsquellen stießen wir auf diese versteinerten Baumstämme, die uns sofort neugierig machten. Zunächst suchten wir nach Abnehmern für Halbfertigprodukte aus diesem Holz, dann fragten wir uns: "Warum sollten wir, die wir diese Stämme suchen, nicht unsere eigenen Produkte herstellen, ohne Bäume zu fällen, und den Charme dieses Jahrtausende alten Holzes zur Geltung bringen". Das war die Geburtsstunde von Teukho. Schon der Name der Marke verweist auf das Wesen der Marke: Er leitet sich aus dem Altgriechischen ab und bedeutet "machen, schaffen, kunstvoll gestalten". Der Name spricht Bände über die Liebe und Leidenschaft für unser Handwerk.
Die reiche Geschichte und das Erbe des versteinerten Holzes ist der Schlüssel zu Ihren Kreationen, eine Verbindung von modernen Elementen und einer von der Zeit geformten Form, die Geschichten aus vergangenen Epochen offenbart. Wie wird diese Art von Holz verarbeitet?
Wir wählen die Stämme direkt an der Quelle aus und überwachen alle Verarbeitungsschritte: vom Schneiden über die Lagerung und Trocknung bis hin zum fertigen Möbelstück. Ich glaube nicht, dass es viele Unternehmen gibt, die von Anfang an eine solche Kontrolle über all diese Schritte haben. Oft entsteht ein neues Produkt, wenn man sich den Stamm ansieht; man kann sagen, dass wir das Stück herausholen, das von Natur aus im Material vorhanden ist. Die bemerkenswertesten Bretter, die nach dem Schneiden zum Vorschein kommen, werden sofort nummeriert und für die Produktion ausgewählt, so dass jeder Tisch aus Teilen eines einzigen Stammes hergestellt wird.
Bei der anschließenden Bearbeitung wird eine Holzprobe an spezialisierte Institute zur Radiokarbondatierung geschickt, wie es bei Fossilien üblich ist. Auf diese Weise können wir jedes Stück mit einem Zertifikat versehen, das den genauen Zeitpunkt angibt, zu dem der Baum gefallen und gestorben ist. Es ist immer wieder aufregend, diese Zertifikate zu erhalten, weil wir wissen, dass wir mit Bäumen arbeiten, die vor mehr als 6.000 Jahren gelebt haben. Was unsere Möbel betrifft, so wählen wir die Bretter persönlich aus, um die richtige Farbkombination zu gewährleisten. Die meisten Teile sind aus Massivholz, in Fällen, in denen das nicht möglich ist, verwenden wir dicke Latten. Einem scharfen Auge fallen sofort die Unterschiede zu anderen vergleichbaren Produkten auf, was uns einen zusätzlichen Wert verleiht. Wir möchten unseren Kunden einzigartige Produkte mit einem modernen Design bieten, bei denen das Holz die Oberhand behält und alle Farbnuancen zeigt, die die Zeit ihm verliehen hat.
Die Lampe Lambda von Luca Degano ist die perfekte Verbindung zwischen der Wärme des Lichts und der des Holzes. Wie kam es zu diesem Entwurf?
Zunächst einmal ist es erwähnenswert, dass die Lambda-Lampe unter den Top 10 der Finalisten des Darc Awards 2020 war, was uns sehr stolz macht, da wir mit weltbekannten Unternehmen konkurrierten. Die Idee basiert auf einem der Werte, die alle Produkte von Teukho kennzeichnen: Zeit. Die Zeit ist die Schlüsseleigenschaft der versteinerten Eiche, die sie veredelt und es uns ermöglicht, all ihre Qualitäten zu schätzen, sowohl visuell als auch taktil. Die Lampe wurde in Zusammenarbeit mit dem Designer Luca Degano konzipiert und entworfen. Ihr Name leitet sich von dem griechischen Buchstaben "λ" ab, der noch heute zur Bezeichnung von Wellenlängen verwendet wird.
Lambda, mit dem in seinem Kern eingebetteten Licht, stellt ein Design von unvergleichlicher, uralter Schönheit dar, das mühelos der natürlichen Form der sinusförmigen Wellenbewegungen der Wellenlängen folgt. Jedes Stück ist ein zeitgenössisches Unikat, das nach den höchsten Standards traditioneller Techniken von Hand gefertigt wird und mit der neuesten LED-Technologie ausgestattet ist. Das fertige Stück strahlt ein warmes, geheimnisvolles Licht aus, das den gesamten Wohnraum erfüllt und die zeitlose Natur der versteinerten Eiche perfekt widerspiegelt. Lambda erzählt eine faszinierende Geschichte für alle, die auf der Suche nach nachhaltigem Luxus sind, ohne die bestehenden Wälder zu schädigen und mit einer Produktion, die die Umwelt nahezu nicht belastet.
Welche Rolle spielt die Nachhaltigkeit bei Ihren Kreationen, und wie sehen Sie die Entwicklung hin zu einer immer "grüneren" Holzverarbeitung?
Wie bereits erwähnt, stammt das von uns verwendete Holz von Bäumen, die durch natürliche Ursachen umgestürzt sind und von Sedimenten begraben wurden, so dass ihnen der Sauerstoff entzogen wurde. Auf diese Weise konnte das Holz über Tausende von Jahren hinweg konserviert werden und die Mineralien des Bodens aufnehmen, wodurch sich seine Farben verändern. Auch die von uns verwendeten Oberflächenbehandlungen sind so umweltfreundlich wie möglich. Wir verwenden mehrschichtige oder laminierte Holzplatten in Übereinstimmung mit den CARB2-Vorschriften nur für die Teile, für die es keine Alternativen gibt. Sie sind zwar teurer als andere Platten, aber aufgrund ihrer größeren Stabilität und Widerstandsfähigkeit sind sie eine zusätzliche Qualitätsgarantie für den Kunden. Auf jeden Fall werden alle unsere Produkte überwiegend ohne Abholzung lebender Bäume hergestellt.
Erfreulicherweise wird heutzutage immer mehr auf Nachhaltigkeit geachtet: Die Abholzung von Wäldern ist nur noch an wenigen Orten weltweit ungeregelt, was wiederum die Umweltbelastung verringert. Auch die verschiedenen Chemikalien, die bei der Verarbeitung verwendet werden, werden zunehmend umweltschonend hergestellt.
CNC-Maschinen sind heute ein fester Bestandteil Ihrer Arbeit. Viele Schritte in Ihrem kreativen Prozess erfordern jedoch handwerkliches Geschick. Was sind das für Momente und warum ist die handwerkliche Komponente so wichtig?
Heutzutage sind CNC-Maschinen zweifellos unverzichtbar für jede Produktion, aber einige Arbeitsschritte erfordern die fachmännische Hand eines Handwerkers. Bei der Anrichte Trigono erfordert die Vorbereitung der Dreiecke für die Türen eine sorgfältige Arbeit bei der Zusammenstellung der Farben, der Überschneidung der Maserungen und der Vorbereitung aller Montageverbindungen. Ohne die Hilfe erfahrener Handwerker wäre dies nicht zu bewerkstelligen.
Letzte Einträge
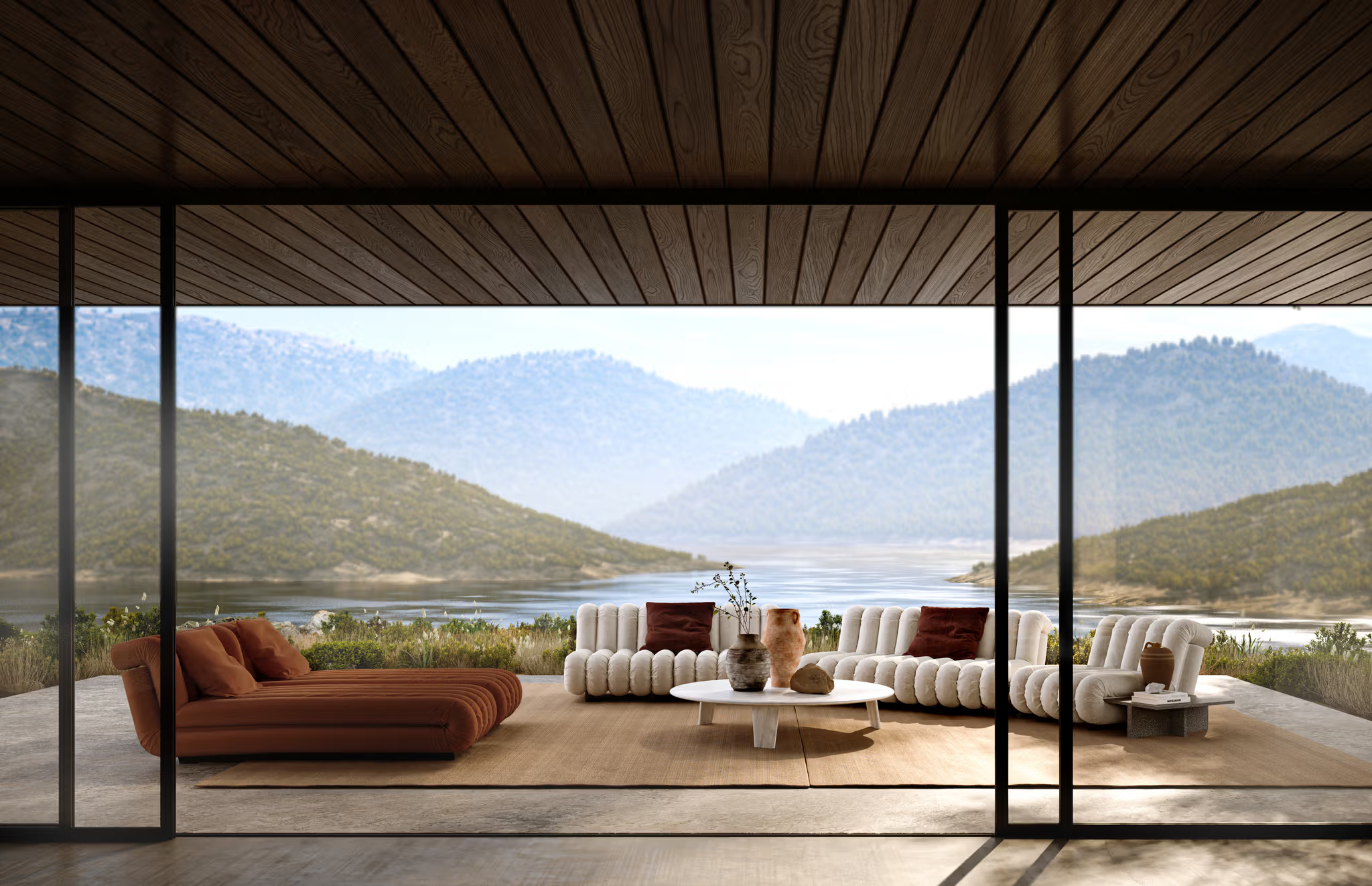
The Artisan
Exteta: Die italienische Lebenskunst in Handarbeit
Exteta wurde im historischen Designviertel von Brianza geboren und lässt sich von der italienische…
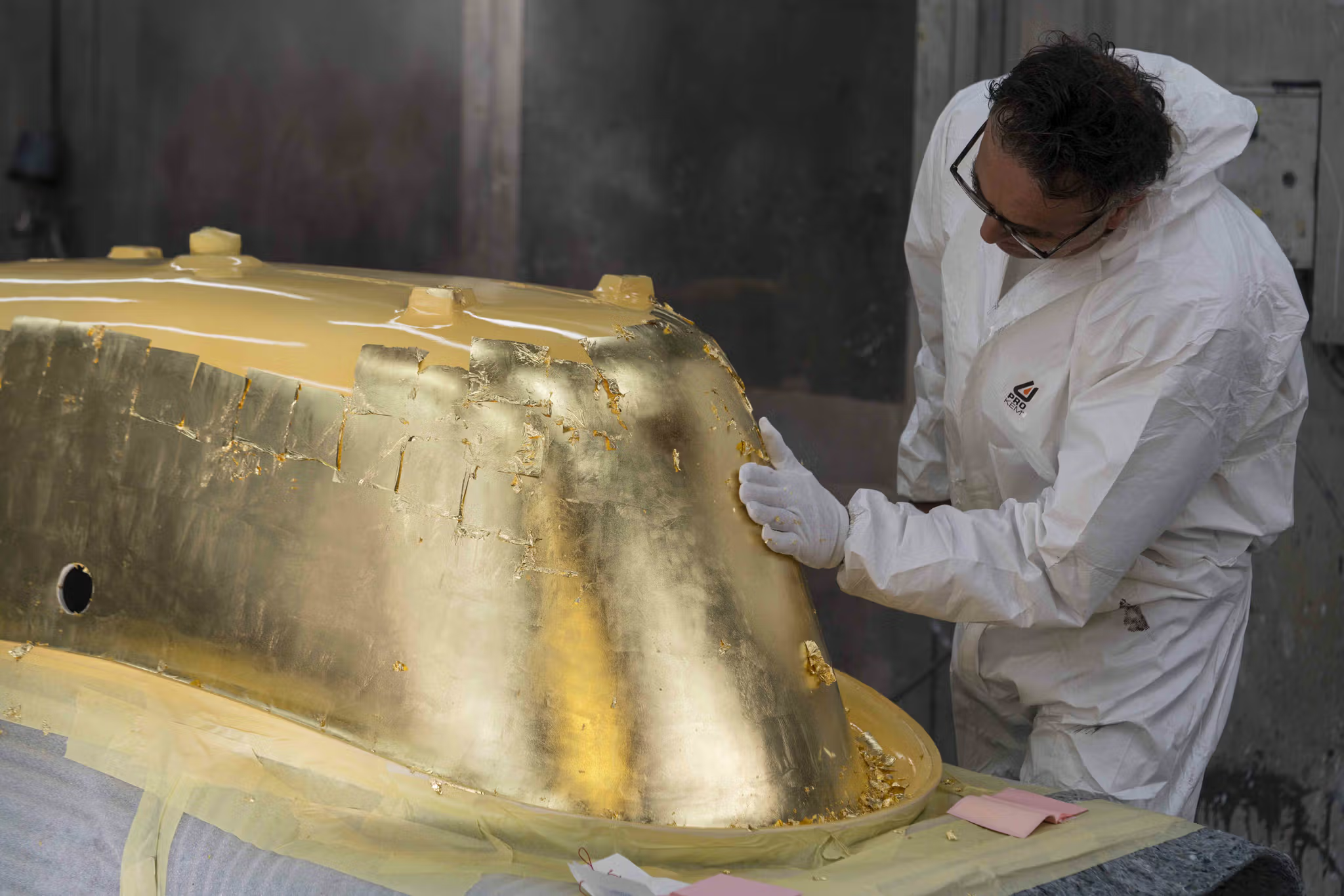
The Artisan
Maßgeschneiderte Inneneinrichtung mit zeitloser Ästhetik von Devon&Devon
Devon&Devon ist ein luxuriöses Design- und Produktionsunternehmen, das sich auf maßgeschneiderte E…